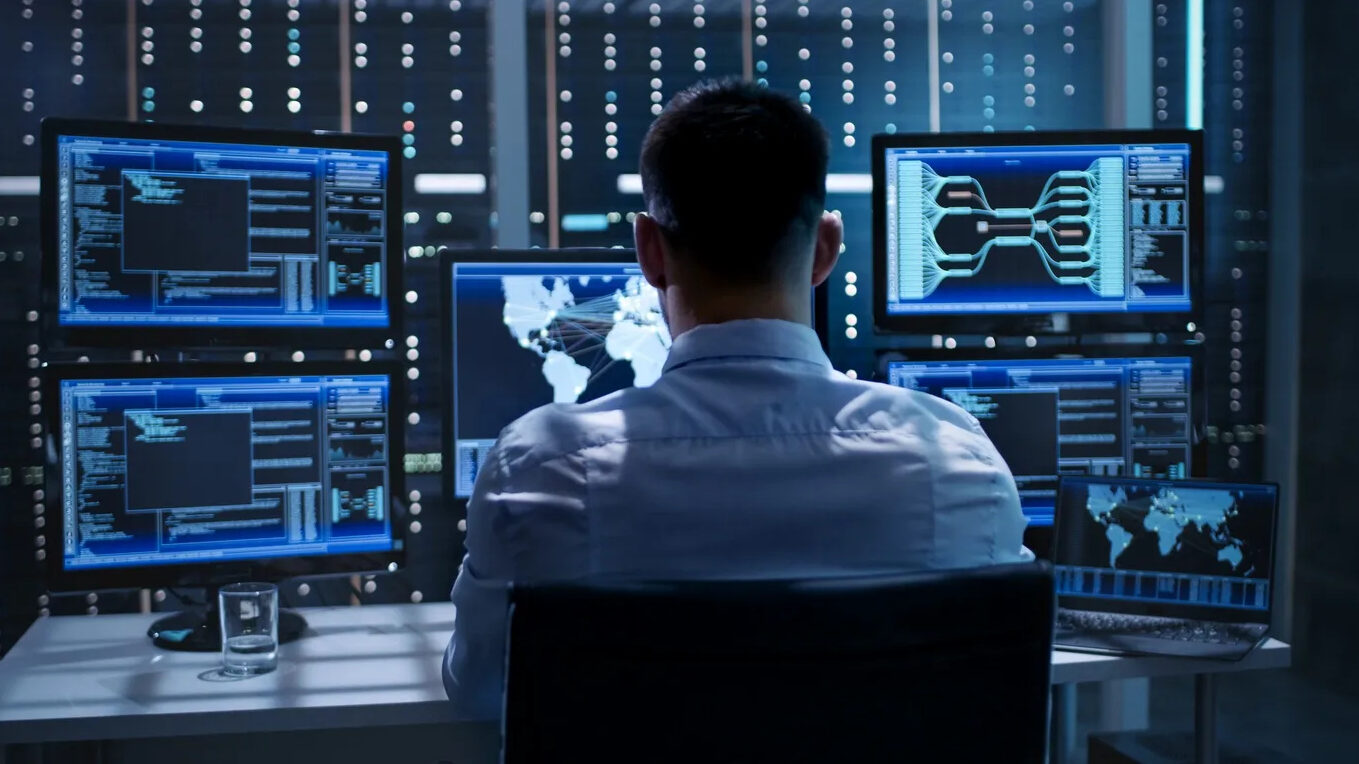
Quality Management Systems
A Quality Management System is a collection of business processes for achieving quality policy and quality objectives to meet customer requirements.

COMPONENTS OF QMS:
- Quality Planning: Defines how to achieve quality goals
- Quality Control: Ensures that processes meet quality standards
- Quality Assurance: Verifies that processes meet quality standards
- Quality Improvement: Continually improves processes to meet quality goals
- Management Responsibility: Management must demonstrate their commitment by showing they can be held accountable for the operations within their organization. They have to ensure that their focus does not deter from the needs of the end user, and that all laws are followed in the manufacturing process. Management has an absolute responsibility to support the quality policy, confirm its alignment with the laws of the country of work, and communicate the mission to employees. They have a responsibility to plan, delegate authority, and communicate effectively. They are also responsible for a periodic review of operations and improvement within the organization, known as the Management Review.
- Resource Management: Top management has a responsibility to ensure that the Quality Management System is compliant and adheres to local regulatory requirements. Top management must ensure that adequate resources are available to perform the work promised by the organization. Providing resources can refer to personnel, infrastructure, consumables, equipment, succession planning, and risk aversion. This can be as specific as controlling the daily workflow to prevent contaminants or ensuring that operations are seamless in years to come with an awareness of looming retirements.
- Product Realization: An organization must plan for the journey from conceptualization to implementation. This can include developing a process for documenting how thoughts are initiated, concepts are verified, and products are designed and developed, as well as how to verify and validate to fulfill the requirements. Communication is critical for the design and development of the device.
- Measurement, analysis and improvement: Development of a procedure for effectively monitoring and measuring product success must include:
- handling complaints
- reporting events to regulatory authorities
- undergoing internal evaluations through auditing
- continual process and product evaluation internally
- identifying and controlling products that don’t meet the original design requirement (nonconforming product)
- analyzing data generated and continually improving the process