Equipment management involves the systematic tracking, maintenance, and optimization of physical assets and equipment throughout their lifecycle. This includes inventory management, preventive maintenance scheduling, repair tracking, and ensuring compliance with safety regulations.
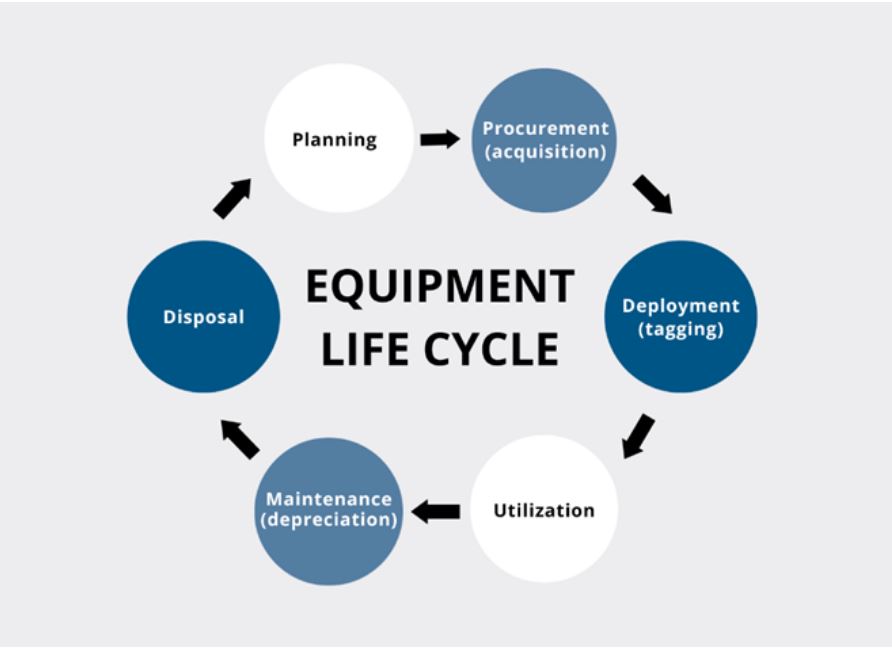
EQUIPMENT MANAGEMENT TASKS
- Purchasing: Buying new equipment
- Maintenance: Scheduling repairs and preventive maintenance
- Inventory: Tracking equipment levels and condition
- Transportation: Moving equipment between locations
- Storage: Keeping equipment in a safe place
- Disposal: Getting rid of old or obsolete equipment
EQUIPMENT PROCUREMENT
1. Requirement Assessment & Planning
- Identify the equipment needs based on manufacturing processes, production volume, and compliance requirements.
- Define user requirements specifications (URS), considering factors like material compatibility, automation level, and regulatory adherence (e.g., FDA, EMA, GMP).
- Conduct feasibility studies and budget planning to align with financial and operational goals.
2. Vendor Selection & Evaluation
- Research potential suppliers with experience in pharmaceutical equipment manufacturing.
- Evaluate vendors based on quality certifications (ISO 9001, GMP compliance, CE marking).
- Conduct audits or factory visits to verify the supplier’s manufacturing and quality control processes.
- Request for Quotation (RFQ) and technical proposals from shortlisted vendors.
3. Technical Review & Compliance Check
- Factory Acceptance Testing (FAT)
- Compare equipment specifications against URS and regulatory guidelines.
- Assess equipment documentation, including validation support, material certificates, and calibration details.
- Ensure the equipment meets cGMP, 21 CFR Part 11 (if software-based), and cleanroom classification requirements.
4. Procurement & Contract Finalization
- Negotiate pricing, delivery timelines, payment terms, and service agreements.
- Establish agreements for after-sales support, spare parts availability, and training.
- Issue a Purchase Order (PO) and ensure all required documentation is in place.
5. Equipment Delivery & Installation
- Coordinate logistics, customs clearance (if imported), and site readiness for installation.
- Site Acceptance Testing (SAT)
- Perform incoming inspection to verify compliance with specifications.
- Supervise installation and ensure alignment with the facility layout and safety standards.
6. Qualification & Validation
- Conduct Installation Qualification (IQ) to verify correct setup and documentation.
- Perform Operational Qualification (OQ) to ensure the equipment functions as intended under test conditions.
- Carry out Performance Qualification (PQ) by running the equipment under actual production conditions.
- Validate software systems if applicable (Computer System Validation – CSV).
7. Training & Handover
- Train operators, maintenance personnel, and quality assurance teams.
- Establish Standard Operating Procedures (SOPs) and maintenance schedules.
- Conduct final acceptance testing before full-scale production.
8. Ongoing Maintenance & Compliance
- Implement preventive maintenance schedules and periodic calibrations.
- Maintain logs for audits and inspections.
- Regularly update equipment documentation and ensure compliance with evolving regulatory standards.
EQUIPMENT MANAGEMENT SOFTWARE
Equipment Management software plays a critical role in streamlining the Equipment Management process. By automating many of the manual tasks involved in deviation management, the software can help companies identify, report, investigate, document, and resolve deviations more quickly and effectively.